When inspecting products for quality control, the cost impacts of poor inspection system accuracy extend further into a factory’s distribution chain than initially meets the eye. The purpose of this article is to explore the hidden, less apparent cost impacts of poor inspection system accuracy.
The confusion matrix
To structure the identification of costs resulting from poor inspection system accuracy, it is useful to identify the inspection system decision outcomes. The confusion matrix is a tool for assessing inspection system accuracy. The actual state of a product under inspection is denoted by ‘p’ and ‘n’ (see figure below). The presence of a real defect is indicated by ‘p’ for positive. The result of the inspection is denoted by ‘P’ and ‘N’ – a detected defect is indicated by ‘P’. For a simple good / bad inspection system (a binary classifier), there are four boxes in the confusion matrix. The True Positives and True Negatives represent the inspection system correctly detecting the true state of the product under inspection. False Positives refer to the inspection system falsely detecting a defect which is not actually present. False Negatives are when the inspection system fails to identify a real defect in the product. Inspection system accuracy is calculated as the number of True Positives and True Negatives divided by the total.
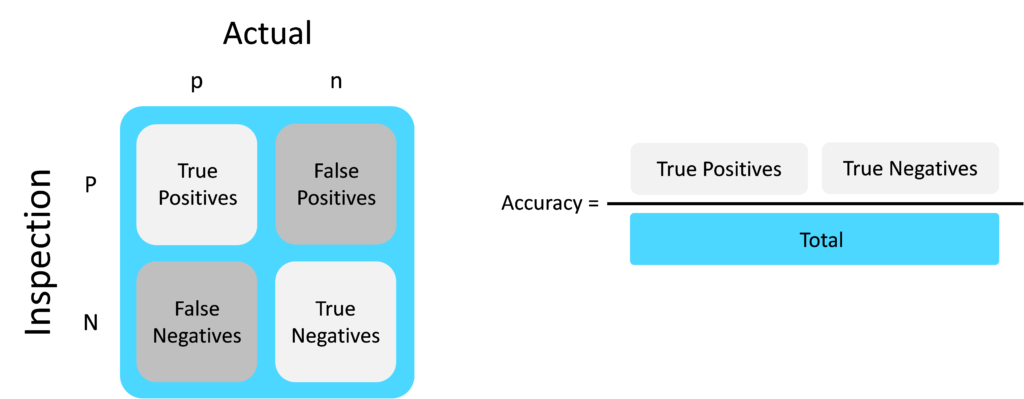
False Positives vs False Negatives
An important concept which is often overlooked when assessing inspection system accuracy is the distinction and relative importance of False Positives vs False Negatives. As the figure below illustrates, False Positives result in unnecessary rework and scrap when good products are identified as having defects. Unnecessary rework and scrap can certainly be very costly however it is not as serious as the opposite scenario (a False Negative), when the inspection system fails to identify a real defect. The impact of False Negatives, also known as ‘quality escapes’, extends all the way down the distribution chain to the retailer and consumer. This can result in wasted distribution space and generate costs associated with processing returns and managing consumer complaints. Even more serious are the defect penalties imposed by retailers and the loss of future sales.
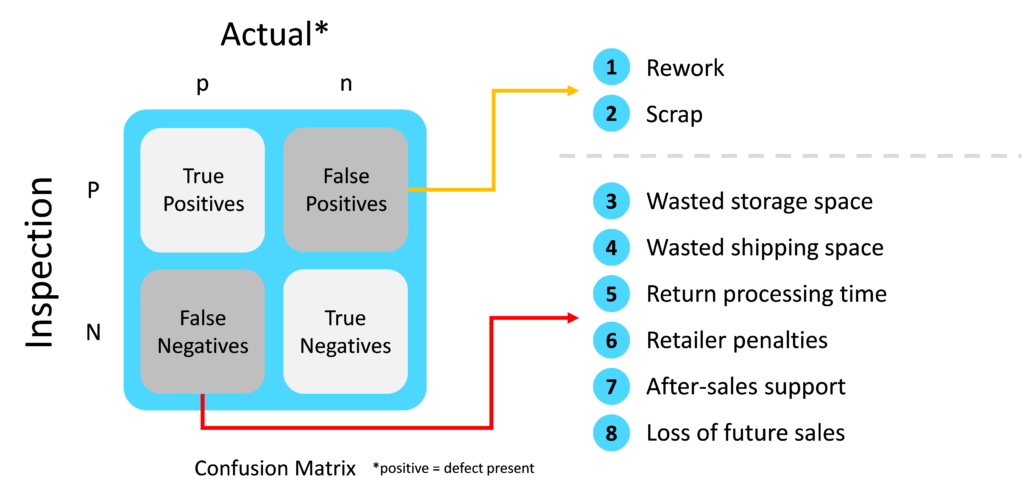
The cost impacts of False Negatives (quality escapes) not only extend further down the distribution chain, they also get more expensive as the defect works its way closer to the consumer. This raises the argument for not only having inspection processes in the Production environment, but also introducing inspection points in Storage & Distribution as a second safety net.
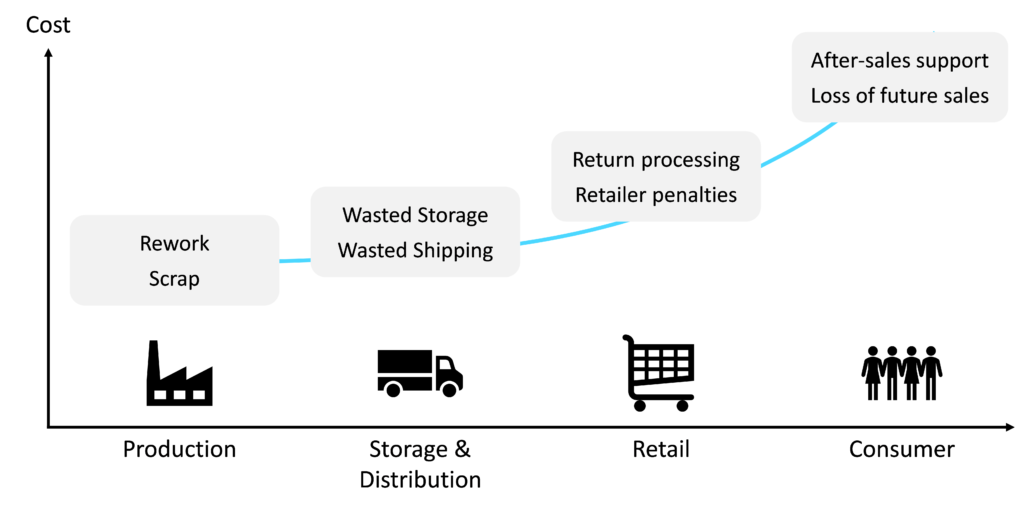
Conclusion
The cost impacts of poor inspection system accuracy often extend far beyond the impacts which are typically considered when calculating ROI (Return on Investment). An important consideration beyond the inspection systems’ raw accuracy performance is the distinction between False Negatives and False Positives, which have significantly different cost impacts.